Arber bergbahn
The Arber Bergbahn relies fully on SNOWsat - on and off the slopes!
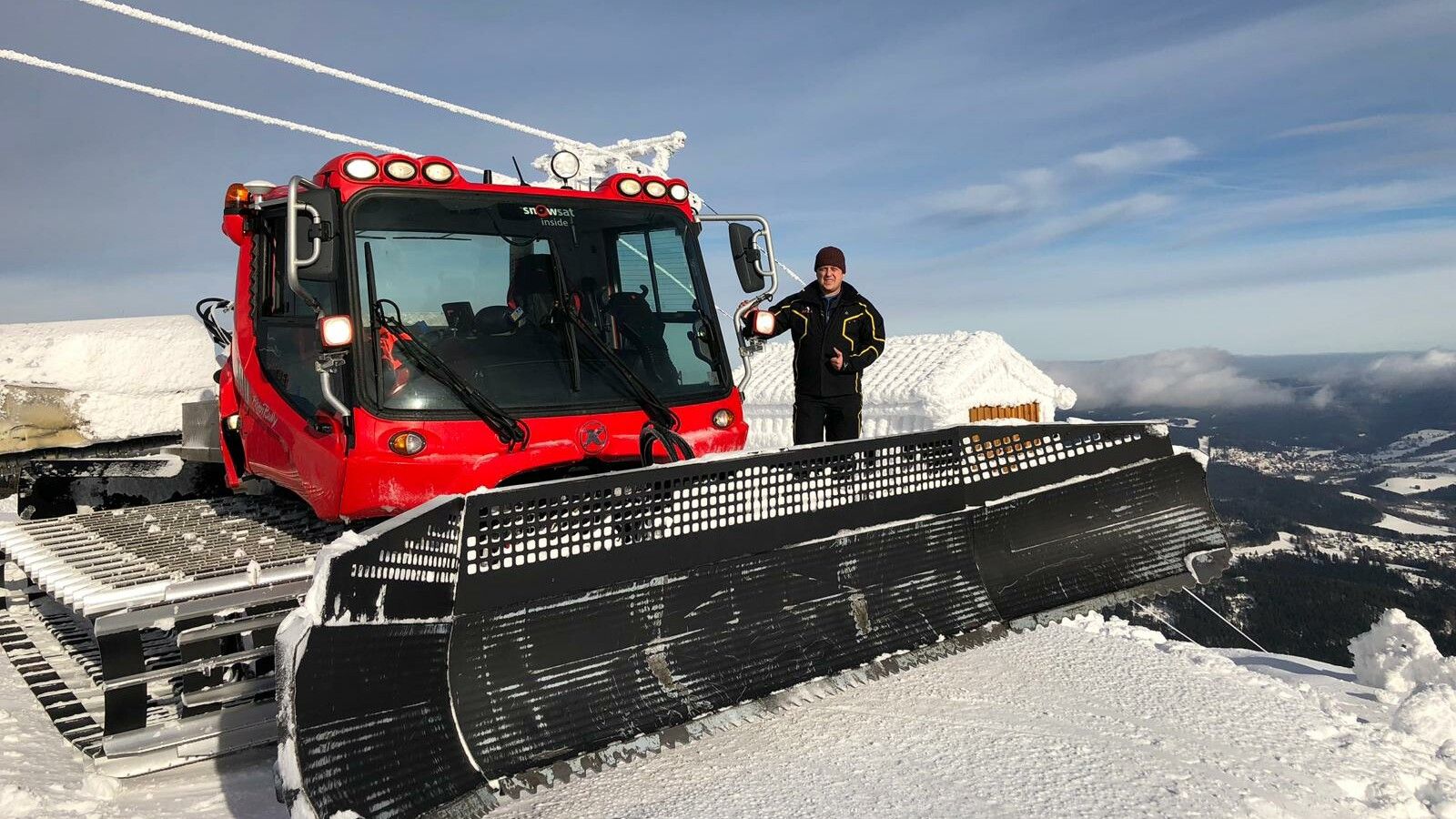
Background
With its 1,456 meters, the Great Arber is the highest mountain in the Bavarian Forest. In summer and winter, the Arber mountain railroad takes (recreational) athletes, families and those seeking relaxation to the highest peak of the Bavarian-Bohemian mountain massif. A six-person gondola lift, two Seichser chairlifts, as well as three surface lifts and four carpet lifts transport visitors directly to snow fun. In addition, 200 kilometers of cross-country ski trails are freshly groomed every day. A total of four state-of-the-art PistenBully vehicles are available for preparing the slopes on the Großer Arber. Three of these vehicles are winch snow groomers. The PistenBully fleet is supplemented by a fully automatic snowmaking system consisting of around 50 snow guns, guaranteeing guests a consistently fantastic skiing experience throughout the entire winter season.
Source: https://www.arber.de/fileadmin/Pressemappe/PR_Arberwinter.pdf
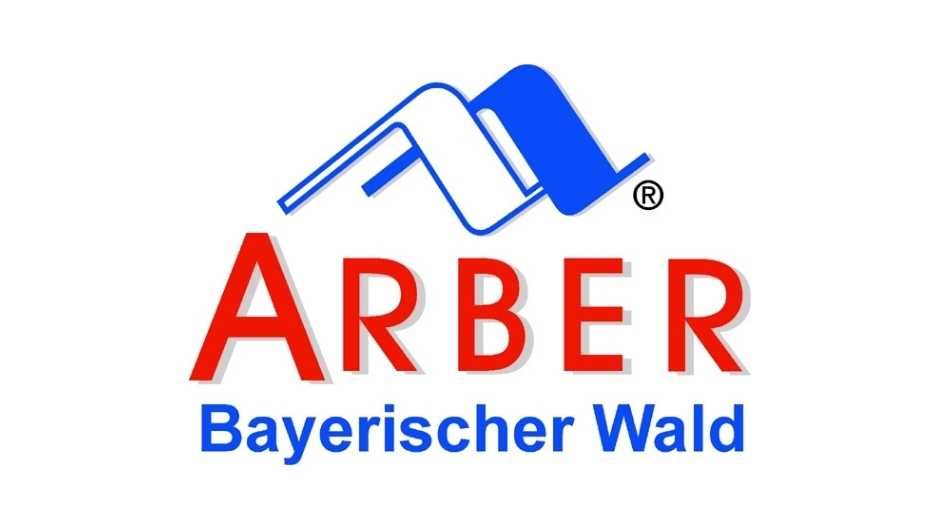
Arber bergbahn
SNOWsat customer since 2017
The following SNOWsat solutions are used:
Maintenance platform for all assets
High precision snow depth measurement
Fleet management solution for all vehicles
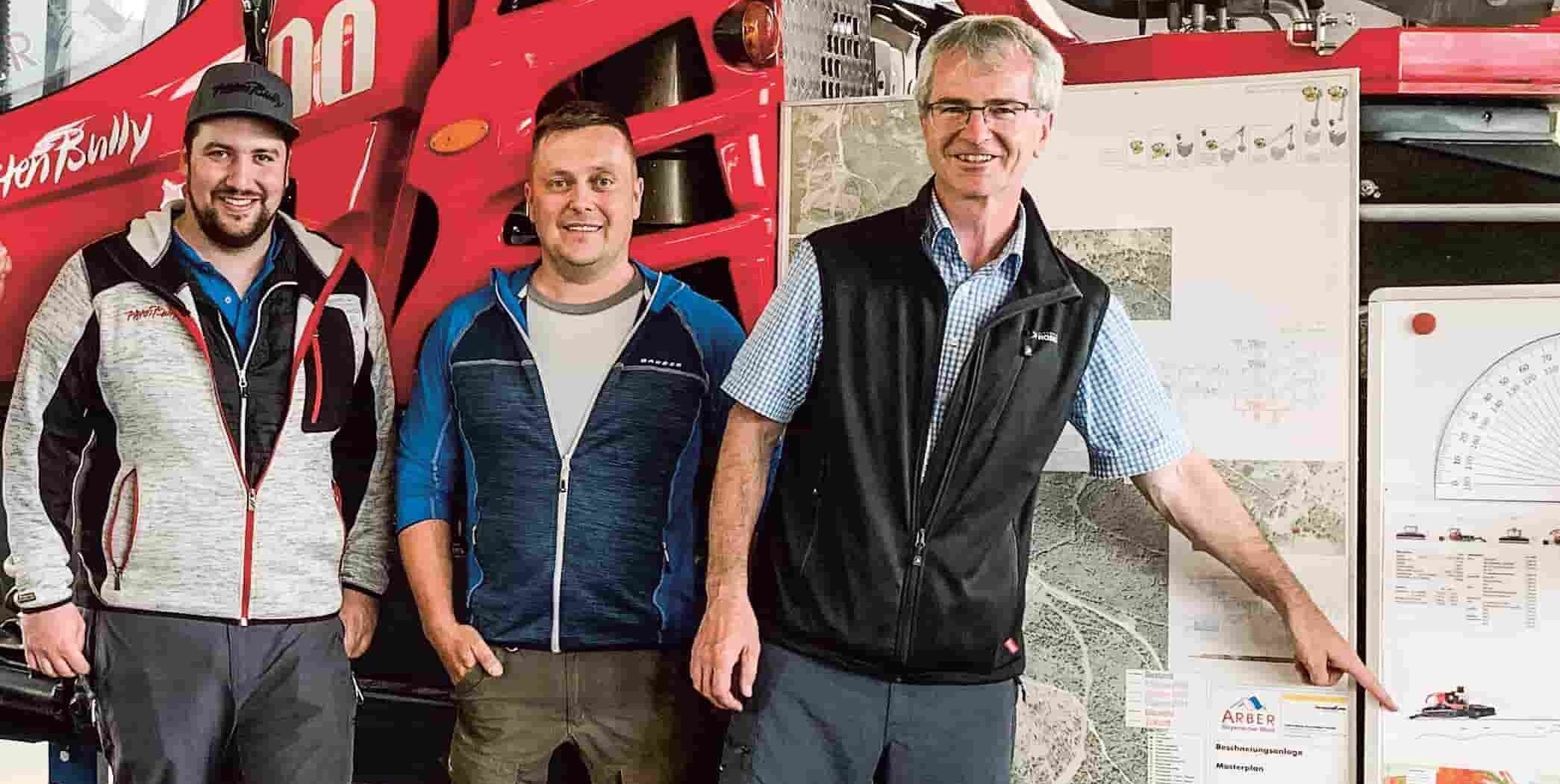
f.l.t.r. Thomas Eckl, Stefan Beywl, Thomal Liebl (Arber Bergbahn)
“With SNOWsat, we can adjust the most minute details in quality that we would never otherwise identify. The precision of the data analysis makes it possible for us to conduct true fine tuning – for instance, regarding the sustainable use of our resources.” - Thomas Liebl
"If in looking at the data you can see for yourself how much room for streamlining there still is in some areas, for example driving in the optimum rpm range, then you want to improve. This is real motivation!” - Thomas Eckl
"SNOWsat does not eliminate communication between the team members but enriches it. A uniform basis of information creates transparency and incorporates all persons involved." - Thomas Liebl
"By using SNOWsat, all of them can see their contribution to the common objective: the ideally groomed slope and happy skiers. Day after day. This motivates employees and gives them a sense of pride." - Thomas Liebl
The quality of the slope must be 100% suitable for the guest
In 2017, this guiding idea motivated Thomas Liebl, Chief Operational Officer of Fürstlich-Hohenzollern- sche Arber Bergbahnen, to opt for SNOWsat.Thanks to the database that SNOWsat provides, is it possible to reveal unused optimization potential throughout the ski area. “With SNOWsat, we can adjust the most minute details in quality that we would never otherwise identify. The precision of the data analysis makes it possible for us to conduct true fine tuning – for instance, regarding the sustainable use of our resources.”
Everyone is a part of the team
In the times of Big Data, the term of “surveillance” plays a central role. At Großer Arber, the position on this is clear: The purpose of SNOWsat is not surveillance. “At the end of every shift, the slope quality has to be correct. Under certain circumstances, it can take even an hour longer,” explains deputy COO Stefan Beywl. And what do drivers think about this? Thomas Eckl does not have to consider this question very long. Nobody feels watched. To the contrary: "If in looking at the data you can see for yourself how much room for streamlining there still is in some areas, for example driving in the optimum rpm range, then you want to improve. This is real motivation!”
The feedback
The COO has received postive feedback from his team as well: “SNOWsat does not eliminate communication between the team members but enriches it. A uniform basis of information creates transparency and incorporates all persons involved. By using SNOWsat, all of them can see their contribution to the common objective: the ideally groomed slope and happy skiers. Day after day. This motivates employees and gives them a sense of pride.”
"Ideas need to be fertilized and watered"
Arber Bergbahnen participated in the development of SNOWsat Maintain from the start. The team accompanied the progress of the digital maintenance management system, from the first workshop during the summer of 2018 to commissioning during the summer of 2019. Liebl esteems teamwork: “Presenting the customer with software without taking the customer’s individual requirements into account is of little use. You have to stay on the ball. You have to fertilize and water an idea for it to bear fruit. At Kässbohrer, we know that they’re on it!”
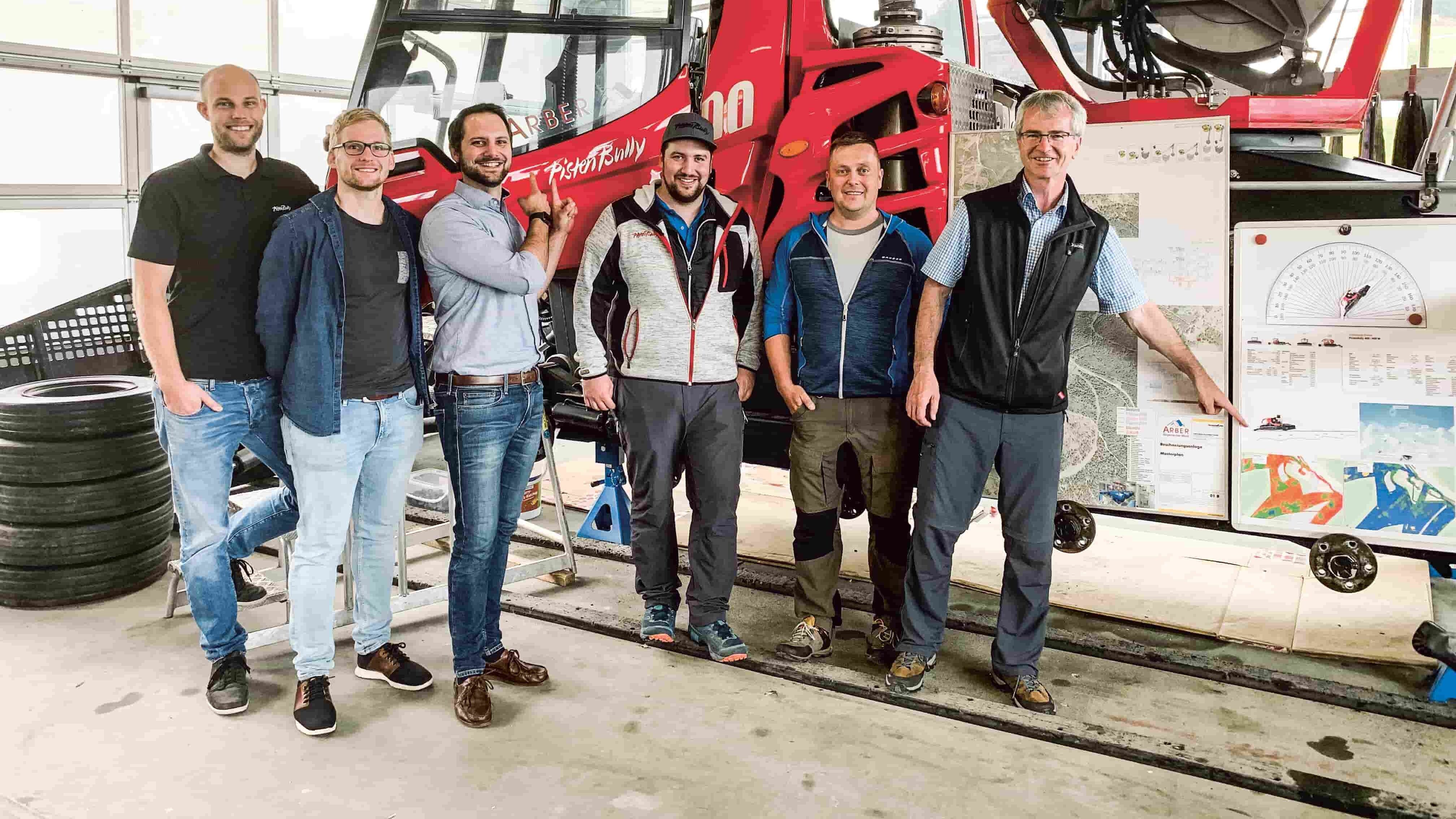
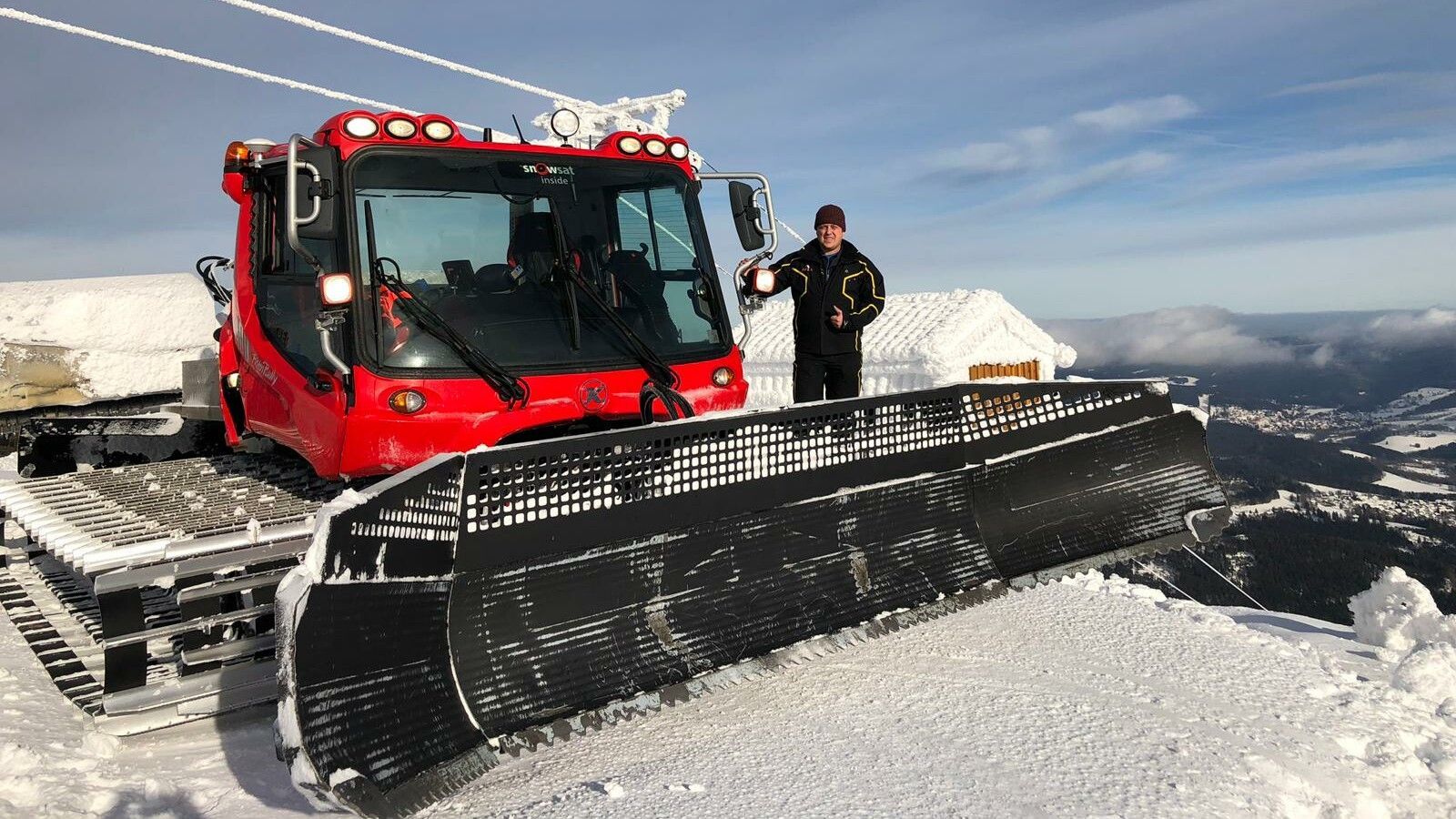
Stefan Beywl, operations manager at Arber Bergbahn, relies fully on SNOWsat.
Write your own SNOWsat success story. Contact your local sales rep now and find out more about SNOWsat solutions!